Przegląd złączy wysokiego napięcia
Złącza wysokiego napięcia, znane również jako złącza wysokonapięciowe, to rodzaj złącza samochodowego. Zazwyczaj odnoszą się do złączy o napięciu roboczym powyżej 60 V i odpowiadają głównie za przesyłanie dużych prądów.
Złącza wysokiego napięcia są stosowane głównie w obwodach wysokiego napięcia i wysokiego prądu pojazdów elektrycznych. Współpracują z przewodami, aby transportować energię z akumulatora przez różne obwody elektryczne do różnych komponentów pojazdu, takich jak akumulatory, sterowniki silników i przetwornice DC/DC. Złącza wysokiego napięcia służą również do zasilania elementów wysokiego napięcia, takich jak przetwornice i ładowarki.
Obecnie istnieją trzy główne systemy złączy wysokiego napięcia: wtyczki zgodne ze standardem LV, wtyczki zgodne ze standardem USCAR oraz wtyczki zgodne ze standardem japońskim. Spośród tych trzech wtyczek, LV ma obecnie największy nakład na rynku krajowym i najbardziej kompletne standardy procesowe.
Schemat procesu montażu złącza wysokiego napięcia
Podstawowa struktura złącza wysokiego napięcia
Złącza wysokonapięciowe składają się zasadniczo z czterech podstawowych struktur: styczników, izolatorów, obudów plastikowych i akcesoriów.
(1) Styki: podstawowe części, które uzupełniają połączenia elektryczne, mianowicie zaciski męskie i żeńskie, styki itp.;
(2) Izolator: podtrzymuje styki i zapewnia izolację między stykami, czyli wewnętrzna powłoka z tworzywa sztucznego;
(3) Obudowa z tworzywa sztucznego: Obudowa złącza zapewnia wyrównanie złącza i chroni całe złącze, czyli zewnętrzną obudowę z tworzywa sztucznego;
(4) Akcesoria: w tym akcesoria konstrukcyjne i akcesoria montażowe, mianowicie kołki pozycjonujące, kołki prowadzące, pierścienie łączące, pierścienie uszczelniające, dźwignie obrotowe, konstrukcje blokujące itp.
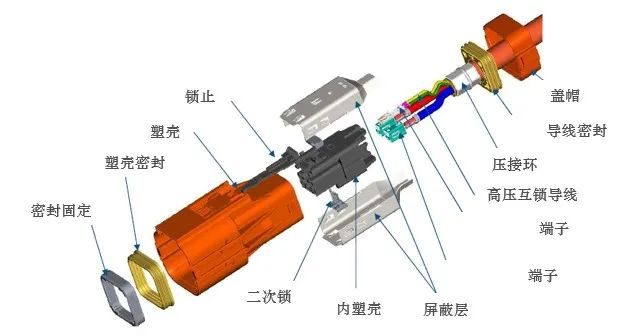
Widok rozstrzelony złącza wysokiego napięcia
Klasyfikacja złączy wysokiego napięcia
Złącza wysokiego napięcia można rozróżnić na wiele sposobów. Klasyfikację złącza można określić na podstawie funkcji ekranującej, liczby pinów itp.
1.Czy istnieje ekranowanie
Złącza wysokonapięciowe dzielą się na złącza nieekranowane i złącza ekranowane, w zależności od tego, czy pełnią funkcję ekranującą.
Złącza nieekranowane charakteryzują się stosunkowo prostą konstrukcją, brakiem funkcji ekranowania i stosunkowo niskim kosztem. Stosowane są w miejscach, które nie wymagają ekranowania, takich jak urządzenia elektryczne w metalowych obudowach, np. obwody ładowania, wnętrza akumulatorów i elementy sterujące.
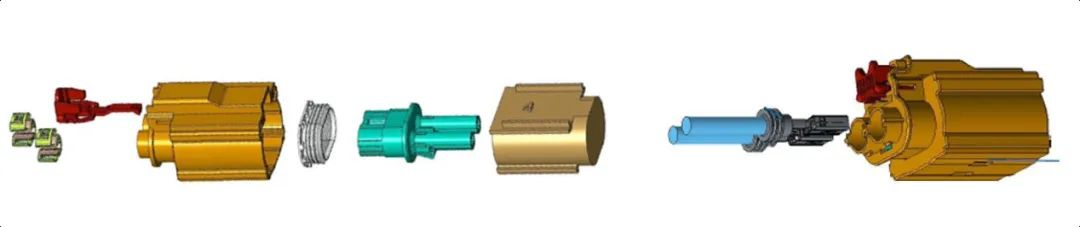
Przykłady złączy bez warstwy ekranującej i bez blokady wysokonapięciowej
Złącza ekranowane charakteryzują się złożoną konstrukcją, wymaganiami dotyczącymi ekranowania i stosunkowo wysokimi kosztami. Nadają się do zastosowań, w których wymagane jest ekranowanie, na przykład tam, gdzie zewnętrzna część urządzeń elektrycznych jest podłączona do wiązek przewodów wysokiego napięcia.
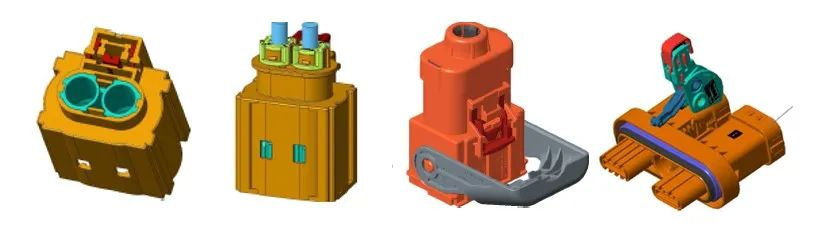
Przykład złącza z osłoną i konstrukcją HVIL
2. Liczba wtyczek
Złącza wysokonapięciowe dzieli się według liczby portów połączeniowych (PIN). Obecnie najczęściej używane są złącza 1P, 2P i 3P.
Złącze 1P charakteryzuje się stosunkowo prostą konstrukcją i niskim kosztem. Spełnia wymagania dotyczące ekranowania i wodoodporności systemów wysokiego napięcia, ale proces montażu jest nieco skomplikowany, a możliwości przeróbek są ograniczone. Złącze jest zazwyczaj stosowane w akumulatorach i silnikach.
Złącza 2P i 3P charakteryzują się złożoną konstrukcją i stosunkowo wysokim kosztem. Spełniają wymagania dotyczące ekranowania i wodoodporności systemów wysokiego napięcia oraz charakteryzują się łatwą konserwacją. Są zazwyczaj stosowane do zasilania wejściowego i wyjściowego prądu stałego, np. w akumulatorach wysokonapięciowych, zaciskach kontrolerów, zaciskach wyjściowych prądu stałego ładowarek itp.
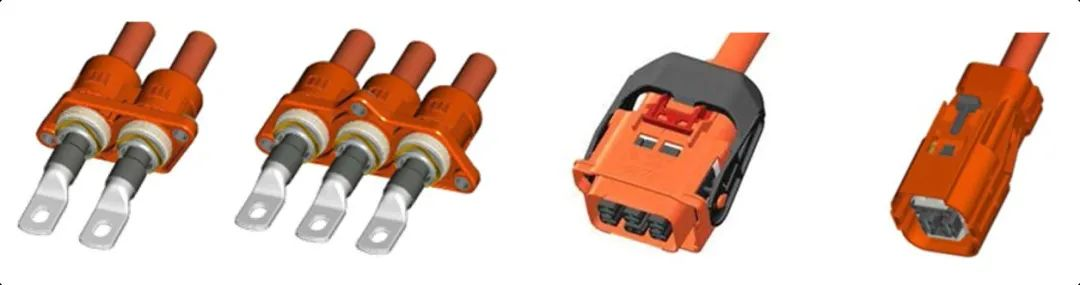
Przykład złącza wysokonapięciowego 1P/2P/3P
Wymagania ogólne dla złączy wysokiego napięcia
Złącza wysokiego napięcia powinny spełniać wymagania określone w normie SAE J1742 i mieć następujące wymagania techniczne:
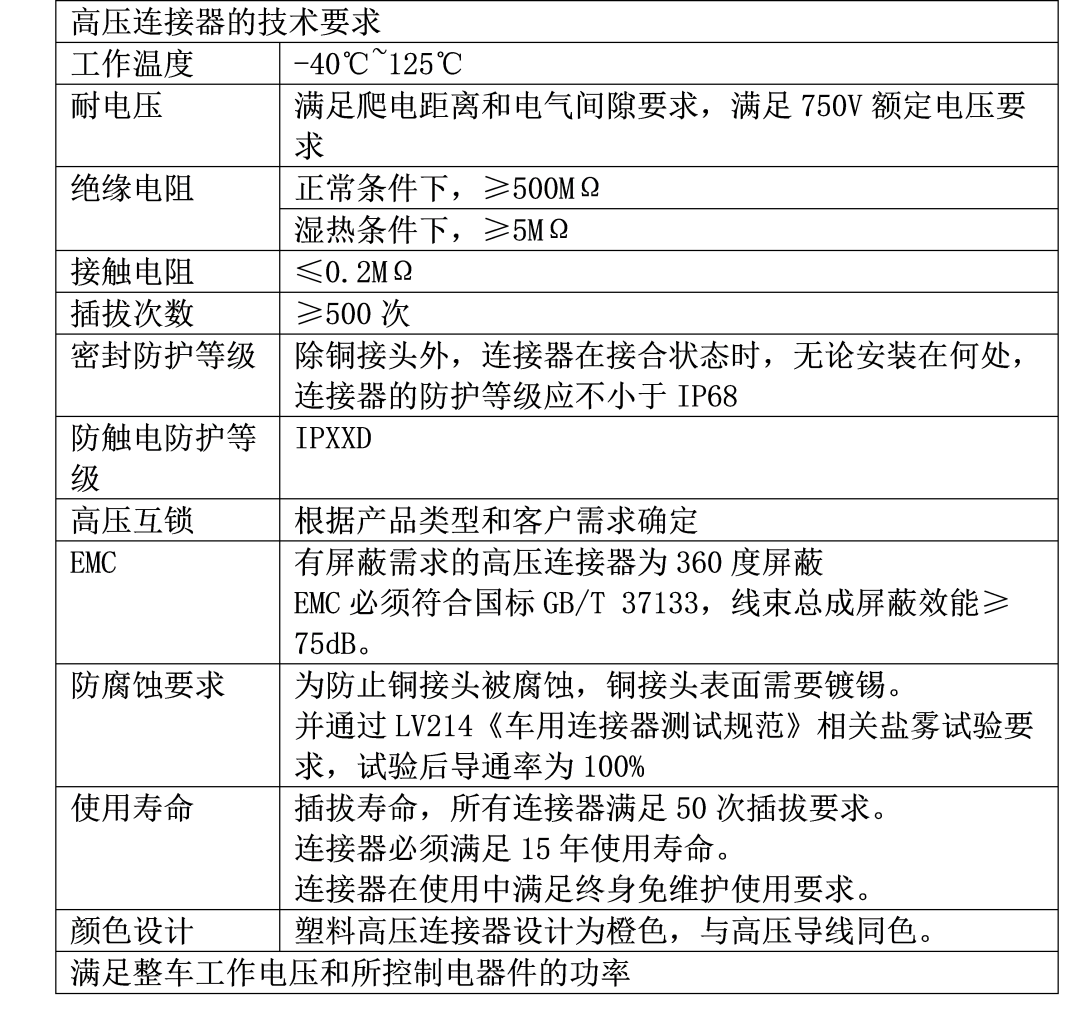
Wymagania techniczne określone w normie SAE J1742
Elementy konstrukcyjne złączy wysokiego napięcia
Wymagania dotyczące złączy wysokiego napięcia w systemach wysokiego napięcia obejmują między innymi: wysokie napięcie i wydajność prądową; konieczność zapewnienia wyższego poziomu ochrony w różnych warunkach pracy (takich jak wysoka temperatura, wibracje, uderzenia, odporność na kurz i wodę itp.); możliwość montażu; dobre właściwości ekranowania elektromagnetycznego; jak najniższy koszt i trwałość.
Biorąc pod uwagę powyższe charakterystyki i wymagania, którym powinny odpowiadać złącza wysokonapięciowe, na początku projektowania złączy wysokonapięciowych należy wziąć pod uwagę następujące elementy konstrukcyjne oraz przeprowadzić ukierunkowaną weryfikację projektu i badań.
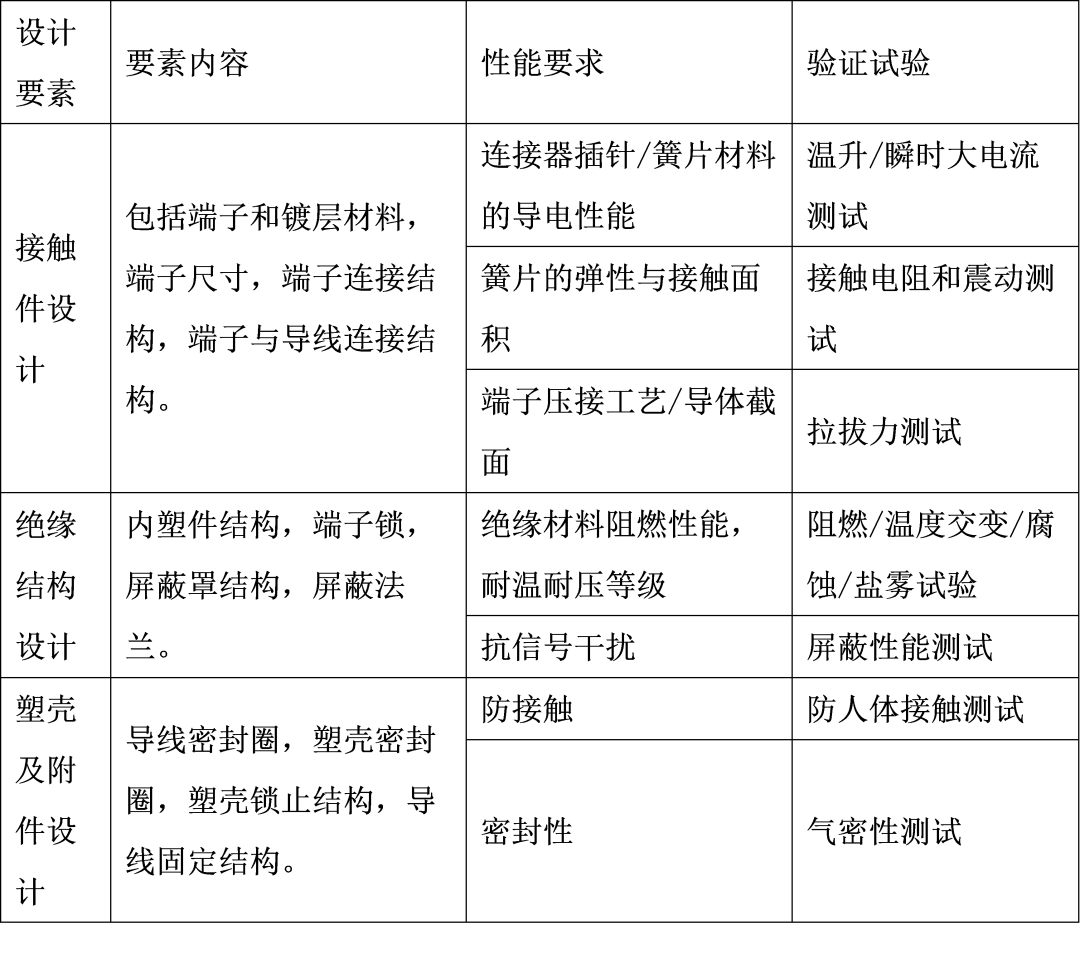
Lista porównawcza elementów konstrukcyjnych, odpowiadających im testów wydajnościowych i weryfikacyjnych złączy wysokonapięciowych
Analiza awarii i odpowiednie pomiary złączy wysokiego napięcia
Aby poprawić niezawodność złącza, należy najpierw przeanalizować jego rodzaj awarii, aby można było podjąć odpowiednie działania zapobiegawcze.
Złącza zwykle mają trzy główne przyczyny awarii: słaby kontakt, słaba izolacja i luźne mocowanie.
(1) W przypadku słabego kontaktu do oceny można wykorzystać takie wskaźniki, jak statyczna rezystancja styku, dynamiczna rezystancja styku, siła rozdzielenia pojedynczego otworu, punkty połączeń i odporność komponentów na drgania;
(2) W przypadku złej izolacji można ocenić jej rezystancję, szybkość degradacji izolatora w czasie, wskaźniki rozmiaru izolatora, styki i inne części;
(3) W celu oceny niezawodności typu stałego i odłączanego można przetestować tolerancję montażu, moment wytrzymałości, siłę zatrzymania sworznia łączącego, siłę wsuwania sworznia łączącego, siłę zatrzymania w warunkach naprężeń środowiskowych oraz inne wskaźniki zacisku i złącza.
Po przeanalizowaniu głównych trybów i form awarii złącza, można podjąć następujące działania w celu zwiększenia niezawodności konstrukcji złącza:
(1) Wybierz odpowiednie złącze.
Wybór złączy powinien uwzględniać nie tylko rodzaj i liczbę podłączonych obwodów, ale także ułatwiać montaż sprzętu. Na przykład, złącza okrągłe są mniej podatne na czynniki klimatyczne i mechaniczne niż złącza prostokątne, charakteryzują się mniejszym zużyciem mechanicznym i są niezawodnie połączone z końcami przewodów, dlatego należy wybierać złącza okrągłe w miarę możliwości.
(2) Im większa liczba styków w złączu, tym niższa niezawodność systemu. Dlatego, jeśli pozwala na to miejsce i waga, należy wybrać złącze o mniejszej liczbie styków.
(3) Przy wyborze złącza należy wziąć pod uwagę warunki pracy urządzenia.
Wynika to z faktu, że całkowity prąd obciążenia i maksymalny prąd roboczy złącza są często określane na podstawie dopuszczalnego ciepła podczas pracy w warunkach najwyższej temperatury otoczenia. Aby obniżyć temperaturę roboczą złącza, należy w pełni uwzględnić warunki odprowadzania ciepła. Na przykład, do podłączenia zasilania można wykorzystać styki znajdujące się dalej od środka złącza, co sprzyja odprowadzaniu ciepła.
(4) Wodoodporne i antykorozyjne.
W przypadku pracy złącza w środowisku z gazami i cieczami powodującymi korozję, aby zapobiec korozji, należy rozważyć możliwość montażu złącza poziomo z boku. W warunkach wymagających montażu pionowego należy zapobiegać przedostawaniu się cieczy do złącza wzdłuż przewodów. Zasadniczo należy stosować złącza wodoodporne.
Kluczowe punkty w projektowaniu styków złączy wysokonapięciowych
Technologia połączeń stykowych koncentruje się głównie na powierzchni styku i sile styku, w tym na połączeniu stykowym między zaciskami i przewodami oraz połączeniu stykowym między zaciskami.
Niezawodność styków jest ważnym czynnikiem decydującym o niezawodności systemu, a także stanowi istotną część całego zespołu wiązki przewodów wysokiego napięciaZe względu na trudne warunki pracy niektórych zacisków, przewodów i złączy, połączenia między zaciskami a przewodami, a także połączenia między zaciskami a zaciskami są podatne na różne awarie, takie jak korozja, starzenie i luzowanie się z powodu wibracji.
Ponieważ awarie wiązek przewodów elektrycznych spowodowane uszkodzeniem, poluzowaniem, odpadnięciem i uszkodzeniem styków stanowią ponad 50% awarii całego układu elektrycznego, należy zwrócić pełną uwagę na niezawodność styków podczas projektowania niezawodności wysokonapięciowego układu elektrycznego pojazdu.
1. Połączenie stykowe pomiędzy zaciskiem a przewodem
Połączenie między zaciskami a przewodami odnosi się do połączenia między nimi poprzez proces zaciskania lub zgrzewania ultradźwiękowego. Obecnie proces zaciskania i zgrzewania ultradźwiękowego są powszechnie stosowane w wiązkach przewodów wysokiego napięcia, z których każdy ma swoje zalety i wady.
(1) Proces zaciskania
Zasada procesu zaciskania polega na użyciu siły zewnętrznej, aby fizycznie wcisnąć przewód w zaciśniętą część końcówki. Wysokość, szerokość, przekrój poprzeczny i siła naciągu zaciskanej końcówki to kluczowe czynniki decydujące o jakości zaciskania, które decydują o jego skuteczności.
Należy jednak pamiętać, że mikrostruktura każdej precyzyjnie obrobionej powierzchni stałej jest zawsze chropowata i nierówna. Po zaciśnięciu końcówek i przewodów, nie chodzi o styk całej powierzchni styku, lecz o styk punktów rozproszonych na powierzchni styku. Rzeczywista powierzchnia styku musi być mniejsza niż teoretyczna, co również powoduje wysoką rezystancję styku w procesie zaciskania.
Zaciskanie mechaniczne jest w dużym stopniu uzależnione od procesu zaciskania, takiego jak siła nacisku, wysokość zaciskania itp. Kontrola produkcji musi być prowadzona za pomocą takich narzędzi, jak wysokość zaciskania oraz analiza profilu/analiza metalograficzna. W związku z tym powtarzalność procesu zaciskania jest przeciętna, a zużycie narzędzia jest duże, a niezawodność przeciętna.
Proces zaciskania mechanicznego jest dojrzały i ma szeroki zakres praktycznych zastosowań. Jest to proces tradycyjny. Prawie wszyscy duzi dostawcy oferują produkty do produkcji wiązek przewodów wykorzystujące tę metodę.
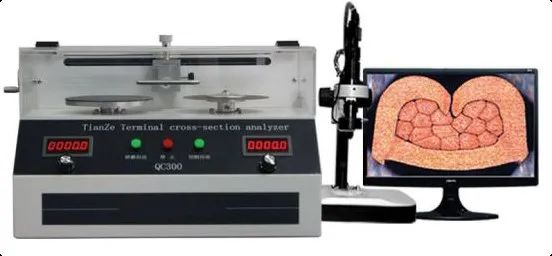
Profile zaciskowe i stykowe przewodów wykonane metodą zaciskania
(2) Proces spawania ultradźwiękowego
Spawanie ultradźwiękowe wykorzystuje fale wibracyjne o wysokiej częstotliwości do przenoszenia energii na powierzchnie dwóch spawanych obiektów. Pod wpływem nacisku powierzchnie dwóch obiektów ocierają się o siebie, tworząc stopienie między warstwami molekularnymi.
Spawanie ultradźwiękowe wykorzystuje generator ultradźwiękowy do przetwarzania prądu o częstotliwości 50/60 Hz na energię elektryczną o częstotliwości 15, 20, 30 lub 40 kHz. Przetworzona energia elektryczna o wysokiej częstotliwości jest ponownie przetwarzana w ruch mechaniczny o tej samej częstotliwości za pośrednictwem przetwornika, a następnie przekazywana do głowicy spawalniczej za pomocą zestawu przetworników, które mogą zmieniać amplitudę. Głowica spawalnicza przekazuje odebrane drgania do spoiny spawanego elementu. W tym obszarze energia drgań jest przekształcana w energię cieplną poprzez tarcie, co powoduje stopienie metalu.
Pod względem wydajności proces spawania ultradźwiękowego charakteryzuje się małą rezystancją styku i niskim nagrzewaniem przetężeniowym przez długi czas; pod względem bezpieczeństwa jest niezawodny i nie poluzuje się ani nie odpada pod wpływem długotrwałych wibracji; może być stosowany do spawania różnych materiałów; jest podatny na utlenianie powierzchni lub powłokę. Następnie; jakość spawania można ocenić, monitorując odpowiednie przebiegi procesu zaciskania.
Chociaż koszt sprzętu do procesu spawania ultradźwiękowego jest stosunkowo wysoki, a spawane części metalowe nie mogą być zbyt grube (zwykle ≤5 mm), spawanie ultradźwiękowe jest procesem mechanicznym i podczas całego procesu spawania nie płynie prąd, więc nie ma problemów z przewodnictwem cieplnym i rezystywnością, które stanowią przyszłe trendy w spawaniu wiązek przewodów wysokiego napięcia.
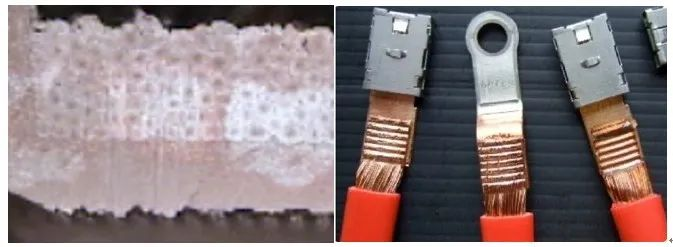
Zaciski i przewody ze zgrzewaniem ultradźwiękowym i ich przekroje stykowe
Niezależnie od tego, czy zaciska się je, czy zgrzewa ultradźwiękowo, po połączeniu końcówki z przewodem, siła odrywająca musi spełniać wymagania normy. Po połączeniu przewodu ze złączem, siła odrywająca nie powinna być mniejsza niż minimalna siła odrywająca.
Czas publikacji: 06.12.2023